Up Polytechnic PT-1 Question paper | Production Technology -1 previous exam paper | Up Polytechnic PT-1 Question paper
Table of Contents
प्रश्न 1- एक स्वच्छ चित्र द्वारा विद्युत प्रक्रम को समझाइये। (U.P.B.T.E. 2012)
उत्तर- विद्युत चुम्बकीय प्ररूपण को चुम्बकीय स्पन्दन प्ररूपण के नाम से भी पुकारते हैं। यह उच्च ऊर्जा द्वारा प्ररूपण की एक विकसित विधि है। विद्युत-चुम्बकीय प्ररूपण के द्वारा धातु चादर के कार्यखण्डों पर आवश्यकतानुसार प्रसार उभारन स्वेजन फ्लेंजन तथा निष्पीड़न इत्यादि संक्रियाएँ की जा सकती है। विद्युत-चुम्बकीय प्ररूपण के अन्तर्गत एक आवरणित प्रेरण कुण्डली की आवश्यकतानुसार या तो कार्यखण्ड पर लपेटा जाता है या फिर कुण्डली को कार्यखण्ड के अन्दर रखा जाता है यदि कार्यखण्ड की धातु को अन्दर की तरफ निष्पीड़ित किया जाना अभीष्ट हो तो कार्यखण्ड पर आवरणित प्रेरण कुण्डली को लपेटा जाता है और यदि कार्यखण्ड की धातु की बाहर की तरफ उभारन किया जाना हो तो कुण्डली को कार्यखण्ड के अन्दर रखा जाता है।
ऐसा इसलिए किया जाता है ताकि उक्त कुण्डली के चारों तरफ उपजाए गए प्रबल व आकस्मिक चुम्बकीय क्षेत्र में कार्यखण्ड को स्थापित किया जा सके। उपरोक्त दोनों ही स्थितियों में से किसी भी स्थिति में कार्यखण्ड को कुण्डली के चुम्बकीय क्षेत्र में स्थापित करके कुण्डली में उच्च क्षणिक विद्युत धारा प्रवाहित की जाती है जिससे प्रबल चुम्बकीय क्षेत्र विकसित होने से कार्यखण्ड की धातु में आवर्त धारा प्रेरित होती है जिसके फल स्वरूप कार्यखण्ड की चादर धातु का निष्पीड़न या उभारन होता है और अन्ततोगत्वा कार्यखण्ड की धातु अभीष्ट आकार बलपूर्वक ग्रहण कर लेती है।
विद्युत-चुम्बकीय प्ररूपण के द्वारा उच्च सुचालकता वाली धातुएँ सुगमता से प्ररूपित की जा सकती हैं। यदि कोई धातु विद्युत कुचालक या निम्न सुचालकता हो तो ऐसी धातु पर उच्च चालकता वाले पदार्थ का लेप चढ़ाकर उनका अभीष्ट प्ररूपण किया जा सकता है।
विद्युत-चुम्बकीय प्ररूपण के गुण
(i) इस प्रक्रम द्वारा धातु ब्लैंक वांछित लहिष्णुता में वस्तु का अभीष्ट आकार प्राप्त किया जा सकता है।
(ii) इस प्रक्रम को सरलता से स्वचालित बनाया जा सकता है।
(iii) इस प्रक्रम द्वारा किसी एक पार्ट को दूसरे पार्ट में बने खांचे या कटावों में फिट किया जा सकता है।
(iv) इस प्रक्रम के द्वारा धातु चादरों पर प्रसारण उभारन, स्वेजन, फ्लेंजन तथा निष्पीड़न इत्यादि संक्रियाएँ की जा सकती हैं।
(v) इसमें अधिक महँगी मशीनरी की आवश्यकता नहीं होती।
Up Polytechnic PT-1 Question paper
प्रश्न 2. फोर्जन क्रिया के अन्तर्गत होने वाले ह्रासों को बताइये। (U.R.B.T.E. 2013)
उत्तर- फोर्जन क्रिया के अन्तर्गत उत्पन्न ह्रासों से आशयप्रत्येक फोर्जन क्रिया चाहे वह हाथ द्वारा हो अथवा मशीन द्वारा, अतप्त अवस्था में हो अथवा तप्त अवस्था में कुछ न कुछ धातु का ह्रास के लिए पर्याप्त छूटे प्रदान की जाती हैं जिसके फलस्वरूप फोर्जन हेतु आवश्यक स्कन्ध का सही आकलन किया जा सकता है।
फोर्जन क्रिया के दौरान विभिन्न प्रकार के सम्भावित ह्रास निम्नांकित हैं
1. कर्तन ह्रास – भण्डार गृहों में रखा हुआ कच्चा पदार्थ सदैव उपलब्ध व्यापारिक आकार में ही होता है जिसे उत्पाद के लिए काटा जाता है। स्कन्ध को आरी के द्वारा काटते हैं। समय धातु का जो ह्रास होता है उसे कर्तन ह्रास कहते हैं। इस ह्रास के लिए पर्याप्त छूट प्रदान की जानी चाहिए।
2. संडासी ह्रास – फोर्जन क्रिया के दौरान स्कन्ध को संडासी में पकड़ना पड़ता है। इसीलिए स्कन्ध को क्रिया के दौरान उचित रूप से पकड़ने के लिए स्कन्ध की थोडी-सी लम्बाई अभीष्ट लम्बाई से अधिक ली जाती है यदि 4 सेमी. की लम्बाई को संडासी में पकड़ना है तो संडासी ह्रास के रूप में स्कन्ध में पर्याप्त छूट प्रदान की जानी चाहिए, जिसकी गणना की जाती है। हस्त फोर्जन द्वारा निर्मित की जाने वाली कुछ वस्तुओं के लिए संडासी ह्रास के लिए कोई प्रावधान नहीं होता है।
3. पपड़ी ह्रास – तप्त धातु की त्वचा की यह प्रवृत्ति होती है कि जब तप्त धातु को वायुमण्डल में खुला छोड़ा जाता है तो धातु त्वचा ऑक्सीकृत होने लगती है। फोर्जन क्रिया के अन्तर्गत हथौड़े के प्रहार के दौरान धातु की ऑक्सीकृत परत पपड़ी के रूप में टूटकर अलग गिर जाती है जिसके परिणाम स्वरूप पपड़ी ह्रास उत्पन्न हो जाता है। इसके लिए स्कन्ध आयतन की 3% ले 5% तक छूट प्रदान की जाती है।
4. चमक हास – जब उत्पाद को डाइयों की सहायता से परिष्कृत किया जाता है तो यकायक चमक उत्पन्न होती है। यह चमक डाइयों के सम्पर्क तल पर प्रतिसारण के कारण उत्पन्न होती है जिसको बाद में छाँटकर पृथक कर दिया जाता है। जिसके फलस्वरूप धातु में चमक ह्रास उत्पन्न होता है। इसीलिए फोर्जित किये जाने वाले नये उत्पाद हेतु छूट के रूप आकलनकर्ता चमक की चौड़ाई व मोटाई को क्रमशः 10 मिमी. व 2 मिमी. की अतिरिक्त विमा की कल्पना करता है। उदाहरण के लिए-यदि डाइयों के सम्पर्क तल पर उत्पाद की परिधि P हो तो चमक का आयतन = (P x 10 x 2) मिमी2 रखा जाता है।
5. स्यू ह्रास – डाइयों के अन्दर फोर्जित किये जाने वाले उत्पादों को प्रक्रमण के द्वारा लगातार प्रचालक द्वारा संडासियों की सहायता से पकड़कर रखा जाता है अतः संडासियों में पकड़े जाने वाले उत्पाद का यही भाग स्यू कहलाता है। जिसे उत्पाद के सम्पूर्तित होने पर काटकर पृथक कर दिया जाता है। डाई फोर्जिंग में अधिकांश इस तरह का स्यू ह्रास पाया जाता है। इसका परास उत्पाद के कुल वजन का 5% से 10% तक होता है।
Up Polytechnic PT-1 Question paper
प्रश्न 3. फोर्जन के अन्तर्गत उत्पन्न होने वाले दोष बताइये। इसके सम्भावित कारण और निराकरण का वर्णन कीजिए।
(U.P.B.T.E. 2014)
उत्तर- फोर्जन दोषों को निम्नलिखित दो वर्गों में वर्गीकृत किया जा सकता है
(i) ऐसे फोर्जन दोष गुहिकायें टीयर्स जली धातु तथा विकाळूरीकरण इत्यादि।
(ii) ऐसे फोर्जन दोष जिनका निवारण आंशिक अथवा पूर्णरूपेण किया जा सके जैसे-अतितापन आन्तरिक प्रतिबल विरूपण उथली दरारें तथा रेशों का शुद्धिकरण इत्यादि।
फोर्जन दोषों के कारण- सामान्यतया फोर्जन दोष निम्नांकित कारणों से उत्पन्न हो सकते हैं।
(i) आधार धातु की गुणवत्ता निम्न कोटि की होना।
(ii) धातुखण्ड का सही प्रकार से गर्म न करना
(iii) फोर्जन की दोषपूर्ण या गलत दशायें जैसे-फोर्जन तापमान का आवश्यकता से अधिक अथवा कम होना।
(iv) दोषपूर्ण या गलत फोर्जन विधियाँ।
(v) फोर्जित धातु का उष्मा उपचार न करना अर्थात् फोर्जित धातु का उपयुक्त अनीलन तथा तापानुशीलन न करना।
(vi) डाइयों का घिस जाना तथा उनका उचित संरेखण न होना।
फोर्जन दोषों का निवारण
(a) गहन दरारें- गहन दरारों को तप्त छैनी की सहायता से भरकर समाप्त किया जाता है। इसकी विधि को पहले बताया जा चुका है।
(b) बारीक दरारें- फोर्जिंग्स की जिन सतहों पर बारीक दरारें हों उन सतहों का अपघर्षण करके दरारों को समाप्त किया जाता है।
(c) विकार्बुरीकृत क्षेत्र- विकार्बुरीकृत क्षेत्र का निवारण भी फोर्जिग्स की सतहों का अपघर्षण करके किया जा सकता है।
(d) यांत्रिक गुणों में सुधार तथा आन्तरिक प्रतिबलों में कमी- इस्पात फोर्जिंग के यांत्रिक गुणों में सुधार लाने तथा आन्तरिक प्रतिबलों को कम करने हेतु फोर्जिंग्स धातु का उपयुक्त अनीलन तथा तापानुशीतन किया जाता है।
(e) विरूपित फोर्जिग्स- पैसों के द्वारा विरूपित फोर्जिंग्स को सीधा करके सुधार लिया जाता है।
Up Polytechnic PT-1 Question paper
प्रश्न 4. तप्त बेलन तथा अतप्त बेलन के दोष व नवारण बताइये। (U.P.B.T.E. 2013, 14)
उत्तर- तप्त बेलन के दोष तथा निवारण
(i) चढ़ाव- बेलन मिल में बेलनों के बीच से धातुखण्ड को गुजारने के अन्तर्गत बेलनों के मध्य के स्थान में धातु के अधिक भराव से यह दोष उत्पन्न हो जाता है। इस चढ़ाव दोष के निवारण के लिए धातुखण्ड का आकार बेलन-पास के आकार से उचित अनुपात में होना आवश्यक होता है।
(ii) दरारें- बेलन क्रिया करने से पूर्व धातुखण्ड की सतह पर यदि दरारें विद्यमान होंगी तो बेलन के पश्चात् बेलित काट में भी दरार दोष काट की पूरी लम्बाई में उत्पन्न हो जायेगा।
अतः इस दोष के निवारण हेतु अपघर्षण चिपिंग या मशीन इत्यादि क्रियाओं की सहायता से बेलन से पूर्व धातुखण्ड की सतह पर दरारों को समाप्त किया जाना चाहिए।
अतप्त बेलन के दोष तथा निवारण
(i) फटन- अतप्त बेलन के अन्तर्गत धातु के कठोर तथा भंगुर हो जाने के कारण धातु चादर या पत्ती पर अतप्त बेलन से यह दोष उत्पन्न हो जाता है। इस दोष के निवारण हेतु बेलन से पूर्व धातु पर अनीलन क्रिया की जानी चाहिए।
(ii) दरारें- इस दोष के उत्पन्न होने का कारण व निवारण के उपाय वे ही हैं जो फटन के लिए हैं।
Up Polytechnic PT-1 Question paper
प्रश्न 5. पात फोर्जन तथा प्रेस फोर्जन में अन्तर बताइए।
उत्तर- पात फोर्जन तथा प्रेस फोर्जन में अन्तर ( U.P.B.T.E. 2010 )
पात फोर्जन | प्रैस फोर्जन |
1. पात फोर्जन में गिरने वाले अंगो की ऊर्जा की अधिकांश मात्रा निहाई तथा धन की नींव में अवशोषित होती है। | 1. प्रैस फोर्जन में गिरने वाले अंगो की ऊर्जा का अधिकांश भाग कार्यखण्ड द्वारा अवशोषित होता है। |
2. पात फोर्जन द्वारा तैयार फोर्जिंग्स कक्ष तथा असममित होती है। | 2. प्रैस फोर्जन द्वारा तैयार फोर्जिग्स सममित परिशुद्ध व चिकनी होती है। |
3. पात फोर्जन में विनिर्माण लागत अपेक्षाकृत अधिक आती है। | 3. प्रैस फोर्जन में विनिर्माण लागत, पात फोर्जन की अपेक्षा कम आती है। |
4. इसमें फोर्जन के उत्पादन की दर अपेक्षाकृत कम होती है। | 4. प्रैसों द्वारा फोर्जन के उत्पादन की दर शक्ति घनों की अपेक्षा अधिक होती है क्योकि इस प्रैस फोर्जन में निष्पीडन क्रिया में उत्पाद सम्पूर्तित हो जाता है। |
5. प्रैसों व उन पर प्रयोग होने वाली डाइयों की अपेक्षा धनों व उन पर प्रयोग होने वाली डाइयो का जीवन कम होता है। | 5. धनों तथा उन पर प्रयोग होने वाली डाइयों की अपेक्षा प्रैसों व उन पर प्रयोग होने वाली डाइयो का जीवन अधिक होता है। |
प्रश्न 6- ड्रॉप फोर्जिंग ड्रोप हैमर तथा प्रेस फोर्जिंग की डाई के बारे में लिखिए। उनके लाभ तथा हानियों का भी वर्णन कीजिए। (U.P.B.T.E. 2013)
उत्तर- ड्रॉप फोर्जिंग – मशीनित व उपघर्षित की हुई डाइयों की सहायता से प्लास्टिक अवस्था तक गर्म की हुई धातु को वस्तुतः गूथने तथा प्ररूपण करने की क्रिया को पात फोर्जन कहते हैं।
पात फोर्जन में प्रयुक्त होने वाली बन्द छाप डाइयाँ दो भागों में निर्मित होती हैं और प्रत्येक भाग में निर्मित की जाने वाली वस्तु के आकर की यथार्थ द्वारा बनी होती हैं, इसीलिए ये डाइयाँ कार्यखण्ड को निश्चित आकार प्रदान करने में सर्वधा सक्षम होती हैं।
पात फोर्जन संक्रिया में इन बन्द छाप डाइयों के मध्य रखी तप्त प्लास्टिक धातु प्रसरण पात धन पुनरावृत्ति प्रहारों के कारण तेजी से होती है। पात घन के पुनरावृत्ति प्रहारों के दौरान बन्द छाप डाइयों में धातु का प्रसरण पूर्ण छाप के साथ होने पर ही वस्तु का सही आकर प्राप्त होगा।
पात फोर्जन घन– पात फोर्जन घन गुरुत्व के सिद्धान्त पर कार्य करता है। टप इस घन का एक मुख्य अंग होता है जो गुरुत्व के अधीन स्वयं अपने भार तथा अपने साथ लगी डाई इत्यादि के भार के कारण किसी निश्चित ऊँचाई से स्वतन्त्र रूप से बलपूर्वक ऊर्ध्वाधरतः नीचे गिरते हुए प्रहार करता है। टप द्वारा प्रदत्त बल का परिमाण उस ऊचाई पर निर्भर करता है जहाँ से रैम नीचे गिरता है। अगले प्रहार के लिए टप को ऊपर उठाने हेतु शक्ति की आवश्यकता पड़ती है जिसके लिए विद्युत मोटर, सम्पीड़ित भाप या सम्पीड़ित वायु का प्रयोग किया जाता है। टप को ऊपर उठाने वाली शक्ति के बन्द छाप डाइयों को निम्नांकित दो वर्गों में वर्गीकृत किया जा सकता है
(i) एकल छाप डाइयाँ
(ii) बहु-छाप डाइयाँ
(a) एकल छाप डाइयाँ– इन डाइयों को एकल छाप डाई इसीलिए कहते हैं क्योंकि इन डाइयों के शीर्ष व पृष्ठ दोनों ब्लॉकों के सैट में फोर्ज की जाने वाली वस्तु की एकल छाप होती है जिसमें वस्तु का अभीष्ट अन्तिम आकार धन के दो या तीन प्रहारों में प्राप्त हो जाता है।
(b) बहु-छाप डाइयाँ– बहु-छाप डाइयाँ के शीर्ष व पृष्ठ खण्डों के एक ही सैट में फोर्ज की जाने वाली वस्तु को अन्तिम परिष्कृत आकार प्रदान करने हेतु सभी छाप तक सभी छापें एक साथ खुदी रहती हैं जिनमें विभिन्न अवस्थाओं में एक साथ एक ही घन के प्रहार से सम्पूर्ण फोर्जन संक्रिया सम्पन्न हो जाती है।
प्रैस फोरजिंग– धन फोर्जन तथा पात फोर्जन में जो डाइयाँ प्रयोग में लायी जाती हैं वही प्रैस फोर्जन में प्रयोग की जाती हैं। अन्तर केवल इतना है कि प्रैस फोर्जन में प्रयोग होने वाली डाइयों में प्रवात कम होता है अत: उनमें अधिक विषय आकृतियों का फोर्जन किया जा सकता है साथ ही अपेक्षाकृत
अधिक वैमायिक यथार्थता प्राप्त की जा सकती है। प्रैस फोर्जन की डाइयों में दोनों ब्लॉकों का परस्पर सरेक्षण बनाये रखना अधिक आसान होता है। घनों तथा उन पर प्रयोग होने वाली डाइयों की अपेक्षा प्रैसों तथा उन पर प्रयोग होने वाली डाइयों का जीवन अधिक लम्बा होता है। प्रेस फोर्जन में चाल, दाब तथा डाई का संचालन स्वतः नियन्त्रित होता है। यही कारण है कि प्रेस फोर्जन में अत्यधिक उच्च कुशलता वाले कारीगरों की आवश्यकता नहीं पड़ती साथ ही उसमें कम्पन्न तथा शोर भी अपेक्षाकृत कम होता है।
प्रश्न 7– हैन्ड फोर्जिंग के स्टॉक में स्केल तथा शीयर हानि की गणना विधि का वर्णन कीजिए।(U.R.B.T.E. 2013, 14)
उत्तर- कर्तन ह्रास-भण्डारगृहों में रखा हुआ कच्चा पदार्थ सदैव उपलब्ध व्यापारिक आकार में ही होता है, जिसे उत्पाद के लिए काटा जाता है। स्कन्ध को आरी द्वारा काटते समय जो ह्रास होता है उसे कर्तन ह्रास कहते हैं। इस हास के लिए पर्याप्त छूट प्रदान की जानी चाहिए।
पपड़ी ह्रास – तप्त धातु की त्वचा की यह प्रवृत्ति होती है कि जब तप्त धातु को वायुमण्डल में खुला छोड़ा जाता है तो धातु की त्वचा ऑक्सीकृत होने लगती है। फोर्जन क्रिया के अन्तर्गत हथौड़े के प्रहार के दौरान धातु की ऑक्सीकृत परत पपड़ी के रूप में टूट कर अलग गिर जाती है जिसके परिणाम स्वरूप पपड़ी ह्रास उत्पन्न हो जाता है। उसके लिए स्कन्ध आयतन की 3% से 5% तक छूट प्रदान की जाती है।
हस्त फोर्जन हेतु अभीष्ट स्कन्ध का आकलन
1. शुद्ध वजन का निश्चय
(i) फोर्जिग का वजन इसकी आरेखन की सहायता से ज्ञात किया जाता है। इस कार्य के लिए पूरी आरेखन का सूक्ष्मता से अध्ययन किया जाता है फिर आरेखन को कुछ निश्चित विमा वाले भागों में विभक्त कर लिया जाता है।
(ii) फिर उपरोक्त विभक्त भागों का आयतन ज्ञात कर लिया जाता है। आयतन में से छिद्रों या कोटरों के आयतनों को घटा दिया जाता है यदि आरेखन में छिद्र या कोटर हो।
(iii) फिर आयतन में धातु के घनत्व का गुणा करके फोर्जिंग का अभीष्ट फोर्जन शुद्ध वजन ज्ञात कर लिया जाता है।
2. कुल वजन का निश्चय – फोर्जिग का कुल वजन का अभिप्राय स्कन्ध की उस मात्रा से है जिससे कि अभीष्ट फोर्जन का निर्माण किया जाना है। फोजिंग के कुल वजन में सम्भावित ह्रासों को (कर्तन, ह्रास, पपड़ी ह्रास, स्यू ह्रास व संडासी हास) को भी सम्मिलित किया जाता है। इस वजन के आधार पर ही स्कन्ध को उपयुक्त लम्बाई तथा उपयुक्त काट में व्यक्त किया जाता है।
3. स्कन्ध का मूल्य – धातु में मूल्य को इसके भार के रूप में व्यक्त किया जाता है, किन्तु आकलनकर्ता इसे सदैव लम्बाई द्वारा व्यक्त करता है इसलिए आवश्यकतानुसार उपरोक्त दोनो ही तरीकों से अर्थात् लम्बाई तथा वजन से प्रत्यक्ष पदार्थ के मूल्य को ज्ञात कर लिया जाता है।
4. प्रत्यक्ष श्रम लागत ज्ञात करना – फोर्जन प्रक्रिया में कार्यरत श्रमिक की मजदूरी के आधार पर प्रत्यक्ष श्रम लागत की गणना की जा सकती है।
प्रश्न 8- बेलन मिलें कितने प्रकार की होती हैं? वर्णन कीजिए। (U.R.B.T.E.2010,11,12,13)
उत्तर- बेलन मिलें मुख्यतः निम्नलिखित प्रकार की होती हैं
(a) दो हाई बेलन मिल (Two High Rolling Mill) – इसमें दो समान भारी क्षैतिज बेलन परस्पर ऊपर-नीचे दो सीधे फ्रेमों की सहायता से बियरिंगों पर टिके रहते हैं। ये दोनों बेलन परस्पर विपरीत दिशा में घूमते हैं। घूमने की दिशा निश्चित होती है। जिसे बदला नहीं जा सकता है। इसका निचला बेलन स्थिर होता है तथा ऊपरी बेलन आवश्यकतानुसार ऊपर-नीचे करके दोनों बेलनों की दूरी को इच्छानुसार कम या अधिक किया जा सकता है। बेलनों के एक दिशा में घूमने के कारण इस मिल के अन्तर्गत धातुखण्ड को केवल एक ही दिशा में प्रभारित करके बेलित किया जा सकता है। वैसे आजकल दो हाई उत्क्रमण मिलें भी बाजार में उपलब्ध हैं जो इसी मिल का विकसित रूप है। दो हाई उपकरण मिलों में एक विशेष प्रकार की चालन यन्त्रावली का प्रयोग करके इसके बेलनों को घूमने की दिशा को बदलकर इस मिल को विकसित किया गया है।

ताकि मिल में धातुखण्ड को आगे-पीछे दोनों ओर से प्रभरित करके बेलित किया जा सके। दो हाई बेलन मिलों पर प्रायः ब्लूमिंग तथा स्लौबिंग क्रियाएँ की जाती हैं। इस मिल के द्वारा सामान्यतया 50 से 150 मिमी. तक मोटे तथा 300 मिमी. से 1500 मिमी. तक चौडे अनुप्रस्थ काट वाले स्लैब बेलित किये जा सकते हैं।
(b) तीन हाई बेलन मिल – इस मिल में तीन क्षैतिज, बेलन एक-दूसरे के ठीक ऊपर लगे रहते हैं। सबसे ऊपरी तथा सबसे नीचे बेलन की घूमने की दिशा समान होती है जबकि मध्य के बेलन के घूमने की दिशा इन दोनों से विपरीत होती है। ये तीनों ही बेलन अपनी निश्चित दिशा में घूमते हैं तथा इनके घूमने की दिशा को बदला नहीं जा सकता है। सबसे पहले धातुखण्ड को सबसे ऊपर तथा मध्य वाले बेलन के बीच एक दिशा में प्रभरित किया जाता है। तत्पश्चात् धातुखण्ड की मध्य तथा सबसे निचले बेलन के बीच में पहले की विपरीत दिशा में प्रभरित किया जाता है। इन बेलनों के बीच में से एकसाथ कई धातुखण्डों को प्रभरित किये जा सकने के कारण इस मिल का प्रयोग विशाल उत्पादन में किया जा सकता है। इस मिल का उपयोग मुख्यतः बिलेट बनाने तथा ब्लूमन में किया जाता है।
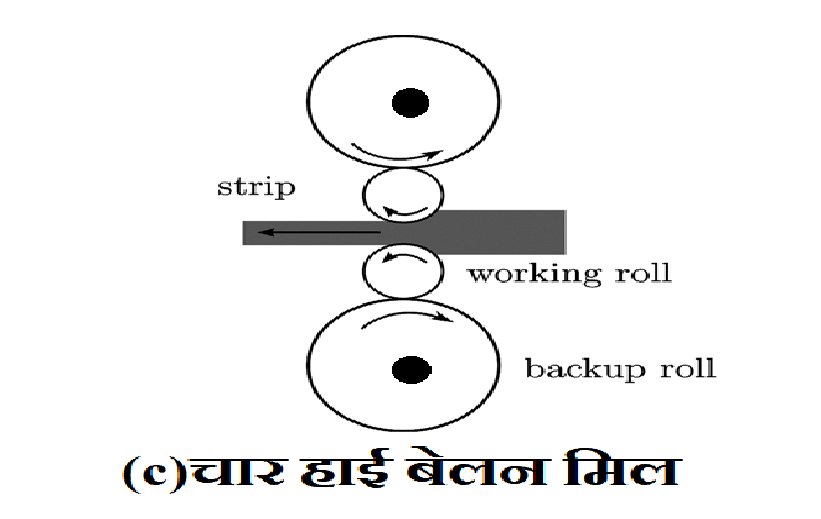
(c)चार हाई बेलन मिल – इसमें चार क्षैतिज बेलन ऊपर-नीचे एक ही ऊर्ध्वाधर तल में लगे रहते हैं। इसमें सबसे ऊपरी तथा सबसे निचले बेलनों का व्यास अधिक तथा बीच वाले दोनों बेलनों का व्यास कम होता है। बड़े बेलनों को सहायक बेलन कहते हैं जिनका मुख्य कार्य छोटे बेलनों के विक्षेप को रोकना हैं। छोटे व्यास वाले बेलन कार्य कारी बेलन कहलाते हैं। जिनका कार्य धातुखण्ड पर पर्याप्त दाब डालना है। इस मिल का उपयोग सामान्यतया पूर्व बेलित स्लैबों
को आगे और बेलित करने में होता है अतः इन मिलों का उपयोग तप्त तथा अतप्त दोनों प्रकार की बेलन क्रियाओं के लिए होता है।
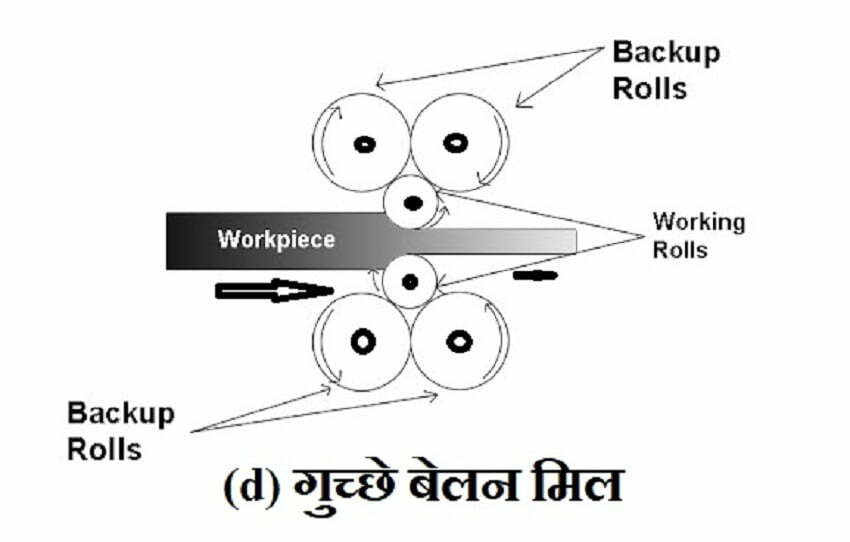
(d) गुच्छे बेलन मिल – इस मिल में छोटे व्यास वाले दो कार्यकारी बेलन होते हैं, जो धातुखण्ड पर सीधे दाब डालते हैं। इन छोटे व्यास वाले बेलनों का विक्षेप रोकने हेतु चित्रानुसार चार या अधिक बड़े व्यास वाले सहायक बेलनों का प्रयोग किया जाता है। इस मिल में सहायक बेलनों की संख्या 20 या इससे अधिक तक हो सकती है। सामान्यतया अतप्त बेलन में इस मिल का उपयोग किया जाता है।
(e) सतत् बेलन मिल – सतत् बेलन मिलों में कई अनुक्रमणीय मिलें एक के बाद एक पास-पास लगी होती हैं ताकि धातुखण्ड एक के बाद एक इन सभी मिलों में से होकर एक ही बार में गुजारा जा सके। इस प्रकार के बेलन मिल में उत्पाद अपनी सम्पूर्ति अवस्था तक पहुँचने तक एक के बाद स्टैण्ड में से सतत् रूप से गुजरता रहता है। यही कारण है कि इस मिल का उपयोग विशाल उत्पादन में किया जाता है। इस बेलन मिल में प्रत्येक स्टैण्ड पर बेलनों की चाल अपने से पहले वाले स्टैण्ड के बेलनों की चाल से अधिक होती है।
प्रश्न 9- बहिर्वेधन को समझाइये तथा इसकी विभिन्न विधियाँ बताइये। (U.R.B.T.E. 2002,04,11)
उत्तर- एक बन्द कक्ष या धारक के भीतर किसी धातु के गर्म किए हुए स्लग या बिलेट को सम्पीड़ित करके डाई के छिद्र से गुजारकर अभीष्ट आकार के उत्पाद निर्मित करने की संक्रिया को बहिर्वेधन कहते हैं। धातुओं के बहिर्वेधन के लिए अधिकांशतः द्रवचालित क्षैतिज प्रैस प्रयोग में लाई जाती है। अधिकांश व्यापारिक धातुएँ एवं उनकी मिश्र धातुएँ जैसे-इस्पात, ताँबा, एल्यूमीनियम, निकिल तथा मैग्नीशियम बहिर्वेधन के सर्वथा योग्य होती है। यह प्रक्रम विशेषकर अलौह धातुओं तथा मिश्र-धातुओं के लिए सर्वाधिक उपयुक्त है। बहिर्वेधन के लिए कच्चे माल के रूप में प्रायः 125 मिमी. से 155 मिमी. व्यास तथा 300 मिमी. तक की लम्बाई वाले बिलेटों का प्रयोग किया जाता है। बहिर्वेधन के लिए प्रयुक्त होने वाली पैसें सामान्यतया 250 से 5500 टन की रेटिंग वाली होती हैं। बहिर्वेधन के दौरान कक्ष डाई तथा रैम का पर्याप्त स्नेहन होना परम आवश्यक है।
बहिर्वेधन की विधियाँ- धातुओं के बहिर्वेधन के निम्नलिखित दो बुनियादी तरीके हैं
1. प्रत्यक्ष या अग्र बहिर्वेधन
2. परोक्ष या पश्च बहिर्वेधन
1. प्रत्यक्ष या अग्र बहिर्वेधन – यह विधि सर्वाधिक प्रयोग में लाई जाती है। बहिर्वेधन की इस विधि में बिल्लेट को फोर्जन ताप तक गर्म करके मशीन कक्ष में डालने के पश्चात् इस बिल्लेट पर रैम द्वारा दाब डालकर धातु को डाई के छिद्र में से बाहर निकाला जाता है। बिल्लेट के आकार एवं डाई के अनुप्रस्थ काट पर बहिर्वेधन की लम्बाई निर्भर करती है। बहिर्वेधन भाग को आवश्यकतानुसार विभिन्न आवश्यक लम्बाइयों में काटा जाता है। प्रलम्बित बहिर्वेधित लम्बाइयों को झुकने से रोकने हेतु एक लम्बे आधार की मेज पर टिकाया जाता है। सामान्यतया बिल्लेट की अन्तिम 10% लम्बाई को अबहिर्वेधिता ही छोड़ दिया जाता है क्योंकि इसमें बिल्लेट की पृष्ठ अशुद्धियाँ रहती हैं इसलिए इस अबहिर्वेधित भाग का परित्याग करना ही उचित होता है।
2. परोक्ष या पश्च बहिर्वेधन – यह विधि भी प्रत्यक्ष या अग्र बहिर्वेधन के समान ही होती है, इसमें अन्तर केवल इतना है कि धातु का बहिर्वेधन डाई में से आगे की ओर होने के बजाय प्लंजर के खोखले भाग में से पीछे की तरफ होता है। कक्ष के भीतर बिल्लेट गतिशील न होने के कारण इस विधि में प्रत्यक्ष बहिर्वेधन की अपेक्षा कम बल लगाने की आवश्यकता पड़ती है किन्तु यान्त्रिक दृष्टि से यह उपस्कर अधिक जटिल होता है क्योंकि खोखले रैम या प्लंजर के बीच में उसी आकार के मार्ग बनाने की व्यवस्था करनी पड़ती है, जिस आकार में बहिर्वेधन किया जाना अभीष्ट हो।
Up Polytechnic PT-1 Question paper
प्रश्न 10- संयोजी डाई पर टिप्पणी लिखिए।(U.P.B.T.E. 1998)
उत्तर- संयोजी डाई- संयोजी डाई में भी यौगिक डाइयों की भाँति दो या अधिक संक्रियाएँ प्रैस के एक ही स्टेशन पर रैम के प्रत्येक आघात में एक साथ की जा सकती हैं। भिन्नता केवल इतनी है कि यौगिक डाइयों में दो या अधिक कर्तन संक्रियाएँ ही सम्पन्न होती हैं जबकि संयोजी डाइयों में एक कर्तन संक्रिया के साथ-साथ नमन या कर्षण संक्रिया भी एक ही स्टेशन पर रैम के प्रत्येक आघात में संयुक्त रूप में सम्पन्न की जा सकती है। ये डाइयाँ भी यथार्थ होती हैं तथा यह विशाल उत्पादन के लिए मितव्ययी भी रहता है। चित्र में एक संयुक्त ब्लैकन तथा कर्षण डाई के क्रिया के विभिन्न चरणों को प्रदर्शित किया गया है।
चित्रानुसार ऊपरी डाई ब्लॉक ब्लैकन पंच की भाँति कार्य करता है तथा इस डाई ब्लाक के बीच में कर्षण पंच स्थित होता है। सर्वप्रथम जब ब्लैकन पंच के नीचे की ओर जाता है तो यह सर्वप्रथम धातु चादर का अपरूपण करता है और धातु चादर में से इच्छित आकार का ब्लैंक प्राप्त हो जाता है फिर ऊपरी डाई ब्लॉक के केन्द्र में स्थित कर्षण पंच नीचे की ओर जाता है जिससे ब्लैंक का कर्षण हो जाता है और निचली डाई की कोटर की आकृति के अनुरूप अभीष्ट आकृति का कप बनकर तैयार हो जाता है। इस कर्षण सक्रिया के दौरान ब्लैंकन पंच दाब पैड की तरह कार्य करता है। आघात के अन्त में कर्षित रूप को बाहर निकाल दिया जाता है। ब्लैंकन पंच के ऊपर की ओर जाने के दौरान धातु चादर के आगे सरकाकर निचले डाई ब्लॉक के ऊपर रखकर फिर से उपरोक्त क्रिया पूर्ववत् दोहराई जाती है इस तरह रैम के प्रत्येक आघात में प्रत्येक बार एक नवीन रूप बनकर तैयार हो जाता है।
Up Polytechnic PT-1 Question paper | Up Polytechnic PT-1 Question paper
इसे भी पढ़े…..